- Joined
- Jul 15, 2012
- Messages
- 2,178
Hi Guys,
I've been thinking this through for the past few days and have come up with a solution that I think works but would love to get your guys feed back and suggestions on metal thickness before I start.
First start with some mesh, I'm thinking 13mm squares with a size of around 1400mm x 600mm
For the frame & supports 20 x 6mm Mild Steel Flat Bar (0.94 Kg/m)
To make the frame I would have a piece of flat bar either side of the mesh all the way round. To join the flat bar together I would drill and tap one side and then use some M6 tapered screws. The screws would go through a hole in the mesh holding it in securely. I'd also have some vertical runs of flat bar for extra reinforcement.
I'm also toying with the idea of putting a lift up flap in the middle, though unsure if this would weaken it too much.
To mount it I'd do something like this which looks like it is using the handle screw holes for the 3rd row seats.
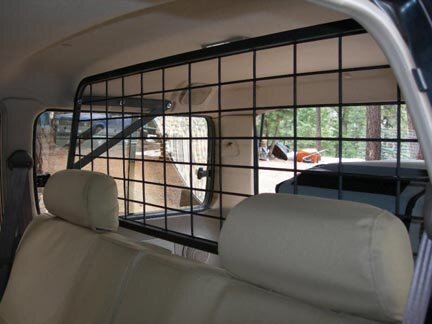
Does this sound workable?
Few things i'm not sure about:
Best mesh size to use
is 6mm flat bar sufficent/overkill. Especially in regards to having enough thread to hold it all together.
How do you think this mesh would work? http://www.screwfix.com/p/apollo-galvanised-welded-mesh-6m-x-0-9m-13mm/53558
Hoping to get away with it for well under £70
I've been thinking this through for the past few days and have come up with a solution that I think works but would love to get your guys feed back and suggestions on metal thickness before I start.
First start with some mesh, I'm thinking 13mm squares with a size of around 1400mm x 600mm
For the frame & supports 20 x 6mm Mild Steel Flat Bar (0.94 Kg/m)
To make the frame I would have a piece of flat bar either side of the mesh all the way round. To join the flat bar together I would drill and tap one side and then use some M6 tapered screws. The screws would go through a hole in the mesh holding it in securely. I'd also have some vertical runs of flat bar for extra reinforcement.
I'm also toying with the idea of putting a lift up flap in the middle, though unsure if this would weaken it too much.
To mount it I'd do something like this which looks like it is using the handle screw holes for the 3rd row seats.
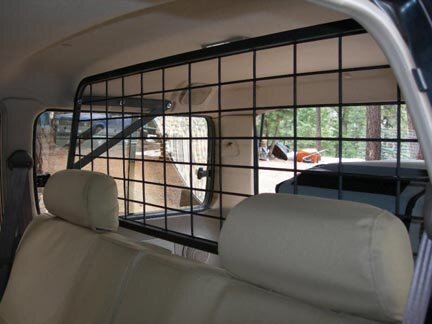
Does this sound workable?
Few things i'm not sure about:
Best mesh size to use
is 6mm flat bar sufficent/overkill. Especially in regards to having enough thread to hold it all together.
How do you think this mesh would work? http://www.screwfix.com/p/apollo-galvanised-welded-mesh-6m-x-0-9m-13mm/53558
Hoping to get away with it for well under £70