Update............................
I worked out I could move the gearbox forwards by 15mm without altering the cross member too drastically.
Got my spare cross member on the bench ready to be modified.
Clamped it to the bench and prepared to weld some 6mm plate to it.
To weld the other side I clamped a piece of 20mm thick steel plate underneath as I couldnt use the bench top as all the other corners of the top were taken up with the vices and guillotine.
TIG welded it together.
Drilled some new mounting holes 15mm further in.
Into the vice next to elongate the holes with the die grinder.
The new creeper has proven invaluable for working under RJ.
Bolted the cross member on.
(These bolts will all have thick 5mm washers under them which I will weld to the cross member.)
Thats as far as I got on the cross member.
I had some deliveries.
New timing belt.
As I need to alter the pipework to move the clutch slave cylinder from the passenger side to drivers side, I bought a pipe bender, flaring tool and cutter.
I pulled the power steering pump off.
I had actually broken one of the hoses off for the idle up control valve as it was hitting the steering box.
Fortunately it isnt really needed and can cause problems if/when they fail as it pumps power steering fluid into the air intake, so I needed to remove it and blank it off.
Broke the plastic top off.
Which left me this bit to weld up.
Cut it down.
Cleaned it up.
And welded the hole up.
Screwed it back in.
Next I had a look at the radiator/fan situation to make sure it would all fit in the space left in front of the engine.
Bolted the standard 1UZ viscous fan back on.
RJ came with an alluminium radiator which I'm hoping to use as I can easily weld it to modify it.
Unbolted all these bits.
Sat the rad in place.
The fan was a bit too close though really.
Not a problem though, I had a cunning plan! To use a thinner fan off a 2lt which also had much less off set.
(Anyone spot the obvious problem in the pic below?)
It bolted on perfectly.
And provided much more clearance against the rad.
Engine mounts next....................................
Now I was reasonably happy with the position of the engine it was time to look at engine mounts.
My aim was to try and mount the engine using the standard 2lt/22r rubber engine mounts and without welding/altering the chassis, so fully bolt on.
One thing that needed consideration was the engine oil dip stick running right through where the engine mount would normally sit on the chassis.
Pulled it off.
Removed a wheel to give me
slightly better access to the mount.
Still pretty buried though which made this job a lot more difficult than it would have been with clear access.
I could have removed the exhaust manifold which would have helped, but I wanted to make sure the mount I was going to fit would also clear the manifold.
I thought I had enough steel to make the mounts with but I didnt.
Being Christmas eve and a Saturday I was pretty limited with what steel I could get, so in the end I bought the biggest section I could from Bunnings, got some 7mm thick galvanised lintel.
Cut a piece to length to bolt to the chassis.
Drilled it.
Cut and drilled another piece to bolt to the engine.
I now just needed to bolt these bits together.
Like this.
Had to drill a hole through the engine plate for the nut on the engine mount to go through because the engine mount was just too tight with the rubber mount and 2 pieces of 7mm plate.
I managed to get a couple of tacks on it with it bolted to the engine, then I pulled it off ready to fully weld it.
Added another piece of 6mm flat to brace it.
Fully welded it top and bottom.
So I needed 4 fixings in total, 2 to fix the adapter plate to the chassis using the original 2 engine mount holes in the chassis, then 2 more to fix the rubber engine mount to the adapter plate in its new position.
One of these bolts would be behind the center of the rubber engine mount, so I needed to weld a threaded stud to the adapter plate without a bolt head sticking up on the other side.
So the adapter plate bolts to the standard chassis mount first.
Then these 2 get bolted together.
Slid in place and bolted on.
Here you can see where one of the bolts for the new engine mount position goes. It goes through a 30mm hole in the center of the original engine chassis mount, into which I found a 30mm x 3mm thick washer to act as a crush tube in affect, with a big thick square washer on top of that, followed by the nut.
That was that side done and I was even able to refit the dip stick.
Other side next that would prove to be much harder as although the engine is actually spaced further from this chassis rail giving more space, the steering box is in the way meaning most of the work had to be done from below.
Sat the standard mount in position to see how far out the chassis mounts were, to the engine mounts.
Marked out some more of the galvanized flat bar.
Drilled the 10mm holes.
Cut it to length.
Drilled the second plate.
Cut the corners off and welded the threaded M10 stud in.
Bolted it all in position.
What followed next was pretty painful!
Lying on my back trying to tack weld some metal to the horrible galvanized metal that kept spitting at me, resulted in a big molten metal hot rock finding its way through my welding jacket, down my arm and then getting trapped in my jacket against my elbow!
But I did manage to get some pretty shit looking tack welds that miraculously held while I unbolted it all.
Cut some 6mm flat, welded it in and gave it a coat of paint.
Bolted the rubber mount on.
Bolted it in position.
Both done!
Again, a shout out to this little baby, its been so handy!
Back to the engine and I bolted the power steering pump back on, which now clears fine and has plenty of room around it after pushing the engine forwards that 15mm.
Sump next....................
I got the front of the chassis supported on my big axle stands so it was nice and high off the ground.
I could then remove the front springs and jack the diff up to see how much needed cutting off the sump for it to clear.
Marked roughly what needed cutting off.
Removed the sump then drained the last bit of oil out of it.
Cleaned it inside and out and got it on the bench ready for surgery.
The underside is sadly a bit scratched from where I had to drag the Lexus onto the trailer (damn coil overs being set so low).
A bit more measuring and checking.
The bump stops would need spacing down to prevent the sump hitting the diff pumpkin.
But most worrying, it looked like the front prop/drive shaft would be really bloody close to the slave cylinder on the bell housing.
I bolted a shaft on to check.
Yes really bloody close! Too close!
The slave cylinder is in perfect alignment with the prop shaft.
I believe this is a fault with the design of the KS Racing bell housing. I think the Dellows bell housing comes with the option of having the slave cylinder on the left or right. If it had been on the other side then this wouldn't be an issue, but the KS Racing one only comes on that side.
There are a few options I could do to fix the situation, one is to cut that big chunk of alluminium off the side of the bell housing and try and fit a hydraulic throw out bearing instead and this is something I may well end up doing.
For now I'm going to carry on with the rest of the build and com back to it.
Made a cardboard template for the notch in the sump.
Marked the sump.
Cut the sump.
Test fitted it.
Cut a piece of 2mm steel to cap the cut off of with.
Got a few tacks on it, then fully welded it.
Then flipped it over and ran another seem of weld around the inside.
Cut out the drain plug and boss from the cut out bit of sump.
It had been in the wrong place anyway as it was above the front diff previously, I moved to the other end where the oil will have a clear path down to a drain tub.
Drilled it out with a step drill.
Clamped the boss in position.
Welded it on.
Gave the whole sump a good clean followed by a few coats of satin black enamel.
Re-fitted it.
And thats where I'm up to. Lots more to do, but I'm making progress.
*EDIT* I cant seem to get rid of the pics below, they shouldnt be there and every time I delete them they come back. 
@Crispin ?
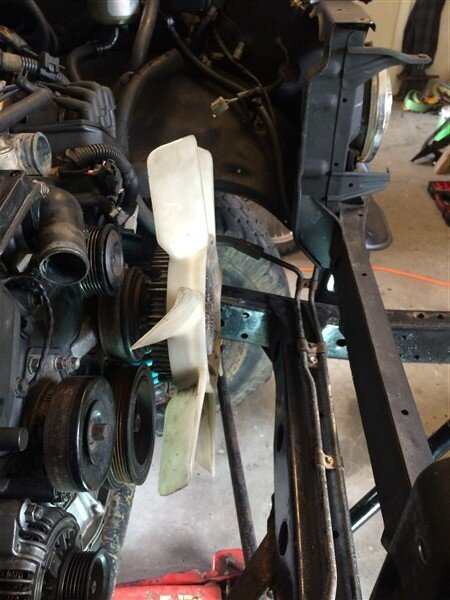